Understanding Plastic Molded Parts in Modern Manufacturing
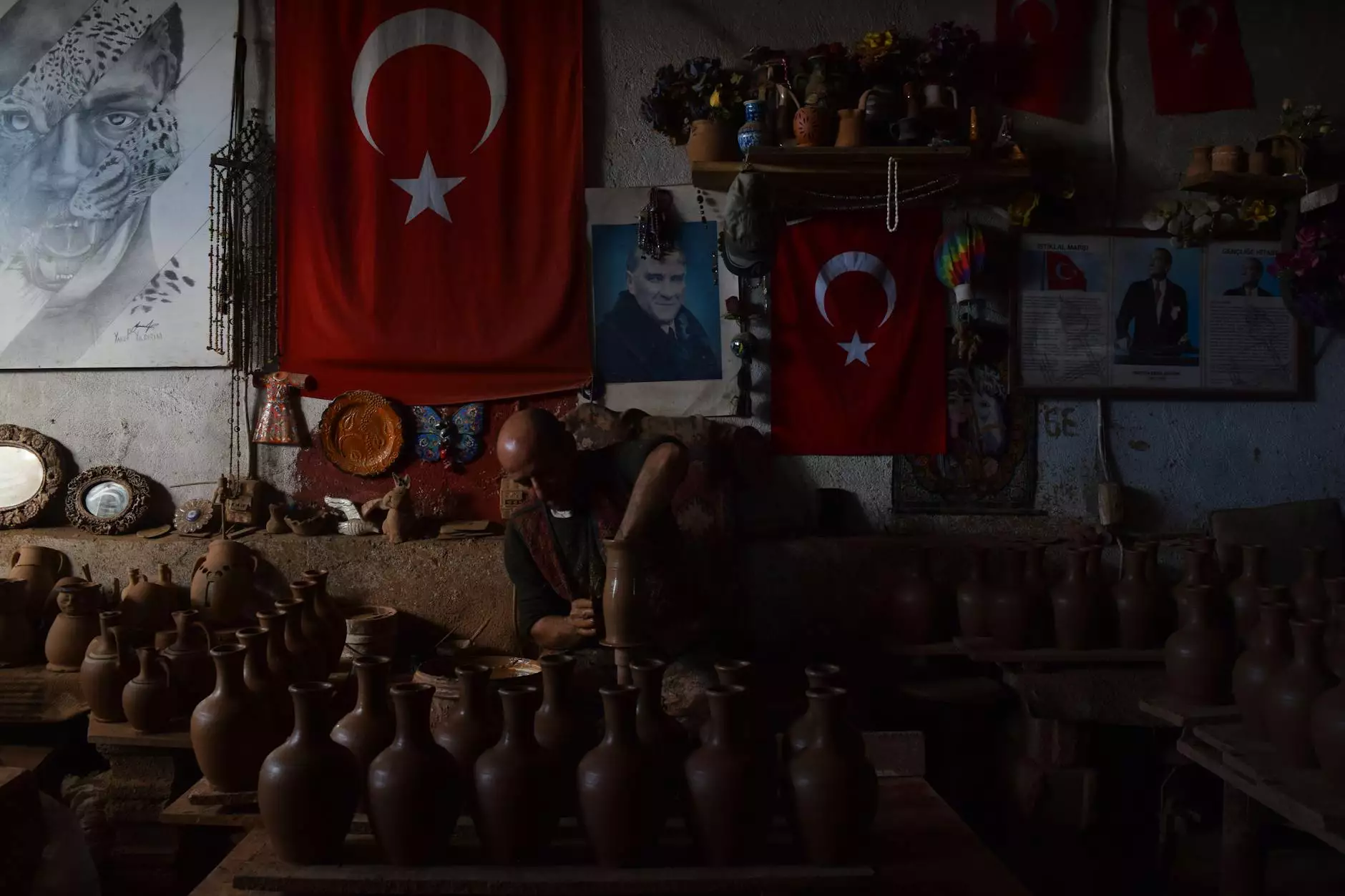
In the ever-evolving landscape of manufacturing, plastic molded parts have emerged as a cornerstone of efficient production methods. Their versatility, cost-effectiveness, and adaptability make them a preferred choice across various industries, from automotive to electronics. This article delves into the significance of plastic molded parts, exploring their design, production processes, and the myriad benefits they offer to manufacturers and consumers alike.
What Are Plastic Molded Parts?
Plastic molded parts are components created by pouring molten plastic into a mold. Once the plastic cools and solidifies, the mold is removed, leaving behind a precisely shaped piece. This manufacturing process is renowned for its ability to produce complex shapes and intricate designs with high precision.
The Plastic Molding Process
The journey of plastic molded parts from conception to production involves several critical steps:
- Design: The initial step involves creating a blueprint of the part, often utilizing Computer-Aided Design (CAD) software to ensure accuracy.
- Mold Creation: Based on the design, a custom mold is fabricated, usually from durable metals capable of withstanding the high temperatures and pressures involved in the molding process.
- Material Selection: Various types of plastic can be used for molding, including thermoplastics and thermosetting plastics, each offering unique properties suited for different applications.
- Molding: The selected plastic is heated until it reaches a molten state and then injected into the mold under pressure. This step is crucial for forming the shape of the part.
- Cooling and Ejection: Once the plastic has cooled and solidified, the mold is opened, and the part is ejected.
- Finishing: Often, additional finishing processes such as trimming, assembly, or secondary operations like welding and machining are applied to achieve the desired quality and performance.
Applications of Plastic Molded Parts
The versatility of plastic molded parts allows them to be utilized across various sectors:
Automotive Industry
In the automotive arena, plastic molded parts are extensively used. They contribute to lightweight vehicle design, enhancing fuel efficiency without compromising safety or performance. Components such as dashboards, panels, and even under-the-hood parts are commonly molded from high-performance plastics.
Consumer Goods
From household appliances to packaging, many consumer products utilize plastic molded parts. The ability to produce parts in various colors and finishes makes them ideal for appealing product designs.
Medical Devices
The medical industry benefits significantly from plastic molded parts due to their ability to be sterilized and manufactured with precision. Items such as syringes, surgical instruments, and medical housing are all commonly produced using this method.
Electronics
Casing for electronic devices, connectors, and insulators often employ plastic molding. The lightweight nature of plastics combined with their electrical insulation properties makes them invaluable in this field.
Advantages of Using Plastic Molded Parts
Manufacturers and designers choose plastic molded parts for various critical reasons:
- Cost Efficiency: Plastic molding offers low production costs, especially in high-volume manufacturing settings. The molds, once created, can produce thousands of identical parts with minimal material wastage.
- Design Flexibility: The molding process allows manufacturers to create complex geometries and detailed designs that are difficult or impossible to achieve with other manufacturing methods.
- Durability and Quality: The materials used in plastic molding can be engineered to provide strong, lightweight parts that resist corrosion, wear, and impact.
- Rapid Production: Once a mold is established, the cycle time for creating parts can be remarkably quick, significantly speeding up production timelines.
- Environmental Considerations: Many plastic materials can be recycled, and advancements in bioplastics are making this industry even more sustainable.
Factors Influencing the Design of Plastic Molded Parts
Creating effective plastic molded parts requires careful consideration of various design factors to ensure functionality and manufacturability:
Material Selection
Choosing the right plastic material is crucial as it affects the performance and durability of the final product. Factors such as chemical resistance, temperature tolerance, and strength are pivotal in this decision-making process.
Mold Design
The design of the mold itself must account for the shrinkage of the plastic as it cools, and the parting line location can impact how easily the molded part can be ejected from the mold.
Wall Thickness
Uniform wall thickness is essential to avoid issues during the cooling process, which can lead to warping or uneven shrinkage.
Tolerances and Finishes
The tolerances required for the part dictate the level of precision in the mold design and part production. Additionally, the desired surface finish can impact the ease of cleaning, aesthetic appeal, and functionality.
The Future of Plastic Molded Parts
As industries continue to seek enhanced efficiencies and sustainability, the future for plastic molded parts is promising. Innovative advancements in materials and production techniques are likely to shape this landscape:
3D Printing Integration
Integrating 3D printing technologies in tandem with traditional molding processes may provide manufacturers with the means to rapidly prototype designs and reduce lead times significantly.
Sustainable Materials
The continuous development of biodegradable plastics and more sustainable manufacturing practices will play a critical role in the evolution of plastic molded parts, addressing environmental concerns while maintaining efficiency.
Smart Technologies
The incorporation of smart technologies into plastic parts, such as embedded sensors for monitoring performance or condition, could revolutionize product functionality and user experience.
Conclusion
In summary, plastic molded parts play a crucial role in contemporary manufacturing, offering unparalleled advantages across numerous industries. From automotive components to medical devices, their ability to meet the demands of modern design and production is undeniable. As technology continues to advance, the future of plastic molded parts looks bright, promising innovative applications and sustainable practices that can reshape the landscape of manufacturing.
For more insights into the world of plastic molded parts and their impact on various industries, visit us at Sumiparts, where we specialize in machining, laser cutting, welding, plastic injection, and vulcanized industrial supplies.